Plastic identification tool
Look by Resin
- Flame Observations(Flame type, Burn type)
- Remarks Observations
Materials | Burns, but extinguishes on removal of flame source | Continues to burn after removal of flame source | |||||
---|---|---|---|---|---|---|---|
Odor | Color of flame | Drips | Odor | Color of flame | Drips | Speed of burning | |
ABS | Acrid | Yellow, blue edges | No | Acrid | Yellow, blue edges | Yes | Slow |
Acetals | - | - | - | Formaldehyde | Blue, no smoke | Yes | Slow |
Acrylics | - | - | - | Fruity | Blue, Yellow tip | No(cast) Yes(molded) | slow |
Type 6 | - | - | - | Burnt wool | Blue, Yellow tip | Yes | Slow |
Type 6/6 | Burnt wool or hair | Yes | - | - | - | Slow | |
PC | Faint, sweet, aromatic ester | Orange | Yes | - | - | - | - |
Polyethylene | - | - | - | Paraffin | Blue, Yellow tip | Yes | Slow |
Polypropylenes | Slow | Yellow | Yellow | Sweet | Blue, Yellow tip | Yes | Rapid |
Polystyrenes | - | - | - | Illuminating gas | Yellow | Yes | Rapid |
ABS/Polycarbonate | - | - | - | b | Yellow, blue edges | No | - |
Polyesters | Hydrochlroic acid | Yellow | No | b | Yellow,blue edges | No | Slow |
Materials | Remarks |
---|---|
PC | Black smoke with soot in air |
Polyethylenes | Floats in water |
Polypropylenes | Floats in water,more difficult to scratch than polyethylene |
Polystyrenes | Dense black smoke with soot in air |
ABS/Polycarbonate | Black smoke with soot in air |
Polyesters | Cracks and breaks |
Look by Burn
- Stops burning when flame removed
- Keeps burning when flames removed
Materials | Burns, but extinguishes on removal of flame source | ||
---|---|---|---|
Odor | Color of flame | Drips | |
ABS | Acrid | Yellow, blue edges | No |
Acetals | - | - | - |
Acrylics | - | - | - |
Type 6 | - | - | - |
Type 6/6 | Burnt wool or hair | Blue, yellow tip | Yes |
PC | Faint, sweet, aromatic ester | Orange | Yes |
Polyethylenes | - | - | - |
Polypropylenes | Acrid | Yellow | Yellow |
Polystyrenes | - | - | - |
ABS/Polycarbonate | - | - | - |
Polyesters | Hydrochlroic acid | Yellow | No |
Materials | Continues to burn after removal of flame source | |||
---|---|---|---|---|
Odor | Color of flame | Drips | Speed of burning | |
ABS | Acrid | Yellow, blue edges | Yes | Slow |
Acetals | Formaldehyde | Blue, no smoke | Yes | Slow |
Acrylics | Fruity | Blue, Yellow tip | No(cast) Yes(molded) | slow |
Type 6 | Burnt wool | Blue, Yellow tip | Yes | Slow |
Type 6/6 | - | - | - | Slow |
PC | - | - | - | - |
Polyethylene | Paraffin | Blue, Yellow tip | Yes | Slow |
Polypropylenes | Sweet | Blue, Yellow tip | Yes | Rapid |
Polystyrenes | Illuminating gas | Yellow | Yes | Rapid |
ABS/Polycarbonate | Yellow, blue edges | No | - | - |
Polyesters | b | Yellow,blue edges | No | Slow |
Look by Float test
Sink/Float test
This test involves dropping small flakes,pellets or chips of plastic(about 1/4-1″sq.) into a jar of water, then shaking the jar. Wait a moment for the pieces to settle out or float.
Plastics that are less dense than water float in water. Most agricultural plastics—including greenhouse and tunnel covers, mulch films, bags from supplements, bale wrap and silage covers, pesticide containers, etc.—are primarily polyolefin’ plastics (polypropylene and the polyethylenes) that float in water.
To differentiate among the polyolefins, fluids with a lower density than water—e.g., alcohol and oil—can be used. Low-density polyethylene (LDPE #4) and polypropylene (PP #5) float in alcohol, while high-density polyethylene (HDPE #2) sinks. Polypropylene—the least dense of the polyolefins—floats even in oil. Try it!
Sink/Float chart
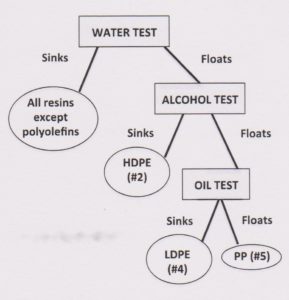
Density of common plastic resins
Plastic Resin | Density g/cm3 at 70°F |
---|---|
POLYEFINS | |
PP(polypropylene,#5) | 0.90 |
LDPE(low density polyethylene,#4) | 0.92 |
LLDPE(linear low density polyethylene,#4) | 0.92 |
Mid-density polyethylene | 0.94 |
HDPE(high density polyethylene,#2) | 0.94-0.97 |
POLYEFINS |
Water | 1.0 |
---|---|
Nylons | 1.02-1.14 |
ABS(acrylonitrile-butadiene-styrene) | 1.05 |
PS (polystyrene),#6 | 1.05 |
Polycarbonate | 1.20 |
PVC(polyvinyl chloride),#3 | 1.29-1.44 |
PET polyester(polyethylene terephthlate),#1 | 1.38-1.39 |
Thermoplastic vs Thermoset discussion
Thermoplastics curing process
Thermoplastics pellets soften when heated and become more fluid as more heat is administered. The curing process is 100% reversible as no chemical bonding takes place. This characteristic allows thermoplastics to be remolded and recycled without negatively affecting the material’s physical properties. There are a variety of thermoplastic resins that offer various performance benefits, but the majority of materials commonly offer high strength, shrink-resistance and easy flexibility. Depending on the resin, thermoplastics can serve low-stress applications such as plastic bags or high-stress mechanical parts. Examples of thermoplastic polymers include polyethylene, PVC, and nylon.
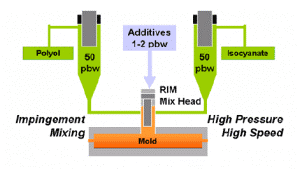
Thermoplastic advantages
➽ High-Impact resistance
➽ Reshaping capabilities
➽ Chemical resistant
➽ Aesthetically superior finishes
➽ Hard crystalline or rubbery surface options
Thermoplastic disadvantages
➽ Expensive
➽ Can melt if heated
Thermoset curing process(Thermosetting plastic)
Thermoset plastics, typically processed by reaction injection molding, contain polymers that combine together during the curing process to form a permanent chemical bond. This process forms weak bonds between the monomer chains within these materials and eliminates the risk of the product remelting when heat is applied, making thermosets ideal for high-heat applications like appliances and electronics.
Thermoset plastics greatly improve the material’s mechanical properties, providing enhanced chemical resistance, heat resistance and structural integrity. Thermoset plastics are frequently used for sealed products due to their resistance to deformation and are also among some of the most impact resistant plastics available. Examples of thermoset plastic polymers include epoxies, phenolics, silicones, and polyesters.
Thermosetting plastic advantages
➽ More resistant to high temperatures
➽ Highly flexible design
➽ Thick to thin wall capabilities
➽ High levels of dimensional stability
➽ Cost-effective
Thermosetting plastic disadvantages
➽ Cannot be recycled.
➽ More difficult to surface finish
➽ Cannot be remolded or reshaped
➽ High levels of dimensional stability
➽ Cost-effective